Intelligent Automation | Oracle | Innovation | IoT | Supply Chain | FMCG | Operations | Manufacturing | Robotic Process Automation (RPA)
Tech Transformation: Mechanization, Automation, and Robotization
Read Time 9 mins | Written by: Praveen Gundala
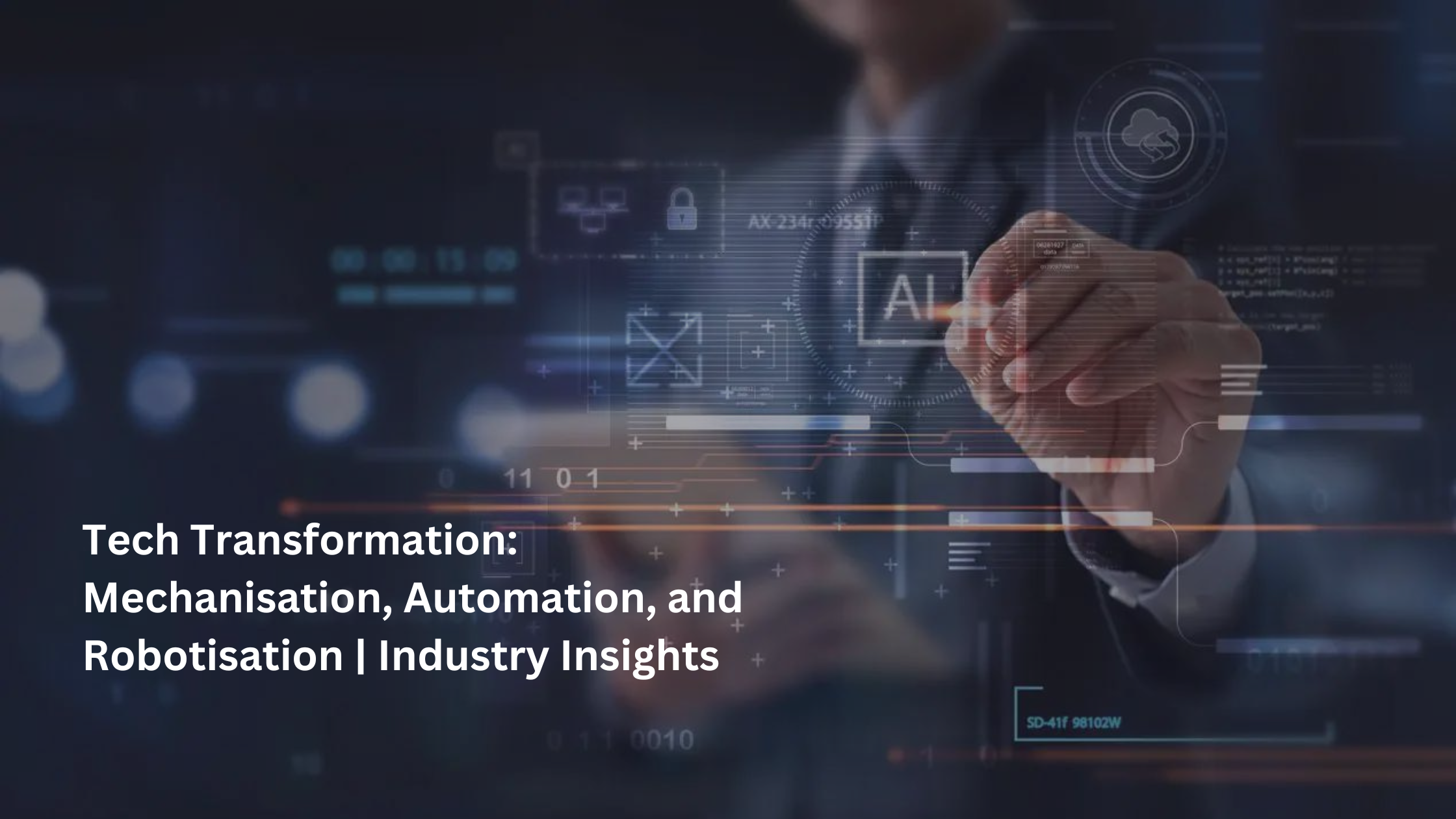
In a time where success is synonymous with efficiency and competitiveness, the incorporation of mechanization, automation, and robotics in warehousing operations has become a pivotal strategy for optimizing the supply chain. This article explores the intricate world of mechanization, automation, and robotics, analyzing the advantages and drawbacks they offer to modern warehouse operations.
The Rise of Mechanisation, Automation, and Robotisation: Exploring the Future of Technology
Mechanisation, automation, and robotisation are rapidly shaping the future of technology. As industries strive for increased efficiency and productivity, the adoption of these technologies has become crucial. Mechanisation involves the use of machines and mechanical devices to replace human labor in performing tasks. This streamlines processes and improves efficiency by leveraging the power of machinery. Automation takes it a step further by using technology to control and monitor the production and delivery of goods and services with reduced human intervention. It aims to create systems that can operate autonomously, leading to increased precision and productivity. Robotisation, on the other hand, focuses on the development and implementation of robots, which are intelligent machines capable of performing complex tasks. These advancements in technology have the potential to revolutionize industries across various sectors and pave the way for a more efficient and advanced future.
Industrial automation and robotics, stemming from 19th-century mechanized industry, have evolved to reduce human control in basic tasks, creating new opportunities and shifting roles towards a white-collar economy. This growth has continued with advancements in artificial intelligence, machine learning, and robot vision, allowing for automation beyond manufacturing to include programming and process organization, enabling a focus on value-added activities. Robots are utilized in physical automation, while virtual tasks and software-based applications do not require their presence.
Mechanization is a cornerstone of modern manufacturing, enhancing efficiency by reducing human labour and increasing production output. By embracing machinery over manual work, businesses can achieve their production targets more efficiently and cost-effectively. This shift towards mechanization sets the stage for automation, where machines can operate independently through mechanical and electrical means. The integration of automation streamlines material handling and transportation processes, cutting down on time-consuming tasks like loading and unloading. Automation also incorporates sensor feedback systems that enable machines to operate autonomously, ensuring precise and efficient manufacturing processes. This evolution towards automation, rooted in the concept of 'Automatos,' has revolutionized manufacturing post-World War II, enabling seamless production with minimal human intervention. Today, the impact of mechanization, automation, and robotization is undeniable, reshaping industries and driving advancements across various sectors. Mechanization empowers businesses to streamline processes and boost efficiency by replacing manual labor with advanced machinery, accelerating production timelines and enhancing overall productivity. Automation and robotization further elevate precision, reduce operational costs, and introduce intelligent machines capable of complex tasks with accuracy and efficiency. These technological advancements are revolutionizing industries and paving the way for a future marked by innovation and efficiency.
Why Automation is Significant?
In the age of the Industrial Revolution, automation encompasses various meanings. For a considerable time, automatic machines have been integral to manufacturing processes. Automation goes beyond mere automatic machines; it involves the integration of mechanical, electrical, and computer-based systems to oversee processes and regulate production. Nearly every machine incorporates some form of automation, albeit to varying degrees based on machine limitations and economic factors. In an automated system, either all processes or a selected few are controlled by self-operated devices known as controllers. The key components of automation include mechanization, sensors, feedback systems, and controllers.
Why is automation necessary in modern production facilities? Let’s find the answer.
- Automation improves productivity significantly. Only one program needs to be set, and the work will proceed without interruption.
- It requires less manpower, reducing labour costs and preventing production floor disruptions due to labour shortages.
- The consistency of production is greatly improved. Automated machines can replicate the same process multiple times, leading to higher production quality.
- Automation also greatly reduces inventory and manufacturing time. Automated machines do not require rest like humans and only need to be shut down occasionally for maintenance, which has minimal impact on production.
- Dependence on skilled operators is significantly reduced through automation. A process can be continued with minimal skilled human involvement, while others can be trained to operate the automated systems.
- With less human effort required, the risk to human life is greatly reduced in automated machining technologies.
There are three main categories of automation:
1. Fixed or Hard Automation:
Fixed automation, also known as hard automation, is primarily used in the production of standardized products such as gears, nuts, bolts, bearings, standard tubes, and washers. It is ideal for manufacturing large quantities of products with slight variations in design. To implement fixed automation, specialized tools, jigs, fixtures, and equipment are essential to achieve the highest production rate and reduce costs significantly.
2. Programmable Automation:
Programmable automation is crucial for manufacturing units producing a variety of products with frequent design changes. This system allows for product design modifications through programs, enabling seamless transitions between manufacturing different products. Programmable automation is suitable for low quantity production units and facilitates small batch production processes. It is commonly utilized by cell phone manufacturers for its flexibility and adaptability.
3. Flexible Automation:
Flexible automation bridges the gap between programmable and fixed automation systems. Utilizing Computer-Aided Design (CAD) and Computer-Aided Manufacturing (CAM), flexible automation, also known as Flexible Manufacturing System (FMS), allows for the production of the same or different products using one unit. Robots play a significant role in flexible automation, enhancing efficiency and reducing human labor. The integration of robots and Computer Integrated Manufacturing (CIM) systems enables the production of a wide range of products with minimal human intervention.
In today's rapidly evolving manufacturing landscape, the use of mechatronics and automation technologies is paving the way for a future where hardware and software concepts are continually evolving to optimize production processes.
The shift from mechanisation to robotisation has completely transformed industries, ushering in a new era of innovation and efficiency. Mechanisation, with its reliance on powerful machines, paved the way for increased productivity and streamlined processes by replacing manual labour. Automation further revolutionized industries by introducing autonomous systems that could operate with minimal human intervention, leading to enhanced precision and cost-effectiveness. Finally, robotisation took technological advancements to new heights with the introduction of intelligent machines capable of handling complex tasks with accuracy and efficiency.
Transforming Industries: A Paradigm Shift
The evolution of traditional warehousing models has been remarkable in adapting to the dynamic and fast-paced market landscape. The integration of mechanization, automation, and robotics signifies a monumental shift from labour-intensive manual processes to cutting-edge, data-driven solutions. These technological advancements hold the promise of transforming the warehousing industry by effectively tackling critical challenges such as labor shortages, escalating operational costs, and the growing demand for swift order fulfilment.
Benefits of Mechanization, Automation, and Robotics:
- Enhanced Efficiency: Automation and robotics usher in a new era of precision and speed in warehouse operations. From order picking to packing and inventory management, tasks are carried out with exceptional accuracy and consistency, minimizing errors and delays.
- Improved Throughput: Mechanized systems and robotic solutions excel in handling high volumes of goods, empowering warehouses to efficiently manage increased order loads and meet peak demand periods with ease.
- Cost Savings: While the initial investment in mechanization and automation may be significant, the long-term cost savings are substantial. Reduced labour expenses, minimized error-related costs, and streamlined processes contribute to a remarkable return on investment.
- Optimized Space Utilization: Automation systems can be customized to maximize the utilization of warehouse space, leading to improved storage density and more efficient use of real estate.
- Safety Enhancement: Robots can take on hazardous tasks, reducing the risk of workplace accidents and creating a safer environment for human workers.
- 24/7 Operations: Mechanized and automated systems enable warehouses to operate continuously, catering to customer demands across various time zones seamlessly.
- Data-Driven Decision Making: Automation generates a wealth of real-time data that empowers informed decisions regarding inventory management, demand forecasting, and process optimization.
- Scalability: Mechanized and automated systems offer the flexibility to scale up or down according to business needs, ensuring warehouses can adapt to changing demands effortlessly.
Navigating the Costs:
- Initial Investment: Implementing mechanization, automation, and robotics requires a significant financial investment for equipment procurement, system integration, and staff training.
- Technological Complexity: Managing and troubleshooting cutting-edge technological systems demands specialized expertise, potentially leading to higher maintenance and support expenses.
- Transition Challenges: Shifting from manual to automated processes may face resistance from the existing workforce, requiring effective change management strategies for seamless adoption.
- Risk of Downtime: System failures or technical glitches could result in operational downtime, disrupting workflow and potentially affecting customer satisfaction.
- Customization Costs: Adapting automation solutions to fit specific warehouse layouts and workflows may entail additional expenses for customization.
- Dependency on Technology: While automation brings efficiency, excessive reliance on technology may expose vulnerabilities in the event of system failures or cyberattacks, highlighting the importance of contingency planning.
The Future of Automation and Robotics
The industrial automation and robotics sector, already valued at billions of dollars annually, is poised for continued growth as technology advances further.
With the increase in robot production, costs have decreased, a trend that is expected to persist as more emerging economies embrace robotics solutions. This uptick in robot availability has also led to a surge in the skills required for their design, installation, operation, and maintenance. Furthermore, the proliferation of software has streamlined engineering processes, making robot programming more accessible and cost-effective.
As technology progresses, robotic systems will evolve to gather data, monitor processes, and troubleshoot issues autonomously. Already adept at utilizing sensors and data points to adjust movements in real-time, robots emulate human craftsmanship to enhance processes and minimize rework or inspection needs.
While robots will continue to automate repetitive tasks, emerging technologies may enable them to respond to voice commands and adapt to a wider range of tasks using artificial intelligence. This potential development could see robots employed in diverse fields like agriculture, where the complexities of locating, assessing, and harvesting crops have posed challenges for automated systems. The precision of robotics is also set to advance, enabling them to perform delicate tasks with enhanced coordination.
Advancements in robotic technology will enable decision-making on which tasks to automate and which should be human-led. With sophisticated safety systems, robots can work alongside humans more seamlessly without compromising safety.
Automated systems are progressing to the point where they can monitor and adjust production line speeds automatically to optimize output and minimize costs.
As these innovations unfold, developing an automation strategy will involve strategically determining which areas to automate and to what extent.
Although industrial automation and robotics are distinct entities, they often work hand in hand to enhance productivity, quality, and safety while keeping costs low across various industries.
Achieving Perfect Harmony:
For a seamless integration of mechanization, automation, and robotics into warehouse operations, a holistic strategy is essential. Balancing the potential benefits with the associated costs and challenges requires a multifaceted approach. Here are some key tactics to strike the perfect equilibrium:
- Comprehensive Evaluation: Delve into a thorough assessment of the warehouse's unique requirements, taking into account factors like order volume, SKU diversity, and workflow intricacies. This analysis is pivotal in identifying the most suitable processes for automation.
- Strategic Financial Planning: Gain a clear understanding of the financial implications, encompassing initial investments, maintenance costs, training expenditures, and potential downtime. Establish a well-rounded budget that considers both immediate costs and long-term savings.
- Effective Change Management: Prioritize strategies for managing change to ensure a smooth transition for the workforce. Implement training programs, foster open communication, and involve employees in decision-making processes to alleviate resistance to technological changes.
- Proactive Risk Mitigation: Develop contingency plans to address potential system failures or disruptions. Incorporate redundancy measures, disaster recovery protocols, and cybersecurity initiatives to mitigate risks effectively.
- Scalability Solutions: Opt for automation systems that can be easily scaled up or down as needed. This adaptability guarantees that the warehouse can adjust to fluctuating market conditions and varying demand levels.
- Collaborative Approach: Engage with independent consultants, subject matter experts, and peers to gather insights into successful automation implementations. Leveraging collective knowledge can empower decision-making and ensure informed choices.
In summary, the fusion of mechanization, automation, and robotics in warehouse operations opens doors to heightened efficiency, enhanced customer satisfaction, and long-term cost savings. While there are challenges and expenses involved in embracing these technologies, a well-planned approach that balances advantages and expenses can pave the way for a competitive edge in today's supply chain environment. The key is to leverage technology's power while staying attuned to the human element crucial for the success of warehouse operations.
From manufacturing lines to precision surgery, the utilization of automation-driven robotics is continuously progressing alongside the expansion of Internet of Things (IoT) connectivity as more companies delve into the advantages of Industry 4.0.
While robots do not necessarily require automation, industrial automation goes beyond physical robots. It encompasses any operation that can be automated by a machine rather than a human, showcasing the diverse virtual components of automation.
Historically, advancements in industry have raised concerns among workers about job displacement due to new technologies. However, as industrial automation replaces mundane, hazardous, or repetitive tasks, it also creates new opportunities for specialization in designing and maintaining automation systems. This shift allows employees to focus on more creative aspects like product design.
The path of industrial automation and robotics is poised for continuous expansion and advancement into uncharted territories, driving down costs as cutting-edge technologies empower intelligent systems capable of real-time data processing and adaptability to changing environments.
These cutting-edge innovations have played a pivotal role in reshaping industries and propelling progress. At FindErnest, we take pride in offering IT solutions and digital innovations that not only enhance business performance but also accelerate time-to-market, boost productivity, and elevate the overall customer experience. Our tailored end-to-end solutions underscore our commitment to delivering exceptional results and guiding businesses towards success through the seamless integration of technology and expertise. Join us on this journey towards a more advanced and efficient future driven by innovation and excellence.
Learn how FindErnest is making a difference in the world of business
Embracing innovation and leveraging technology to drive business transformation
Praveen Gundala
Praveen Gundala, Founder and Chief Executive Officer of FindErnest, provides value-added information technology and innovative digital solutions that enhance client business performance, accelerate time-to-market, increase productivity, and improve customer service. FindErnest offers end-to-end solutions tailored to clients' specific needs. Our persuasive tone emphasizes our dedication to producing outstanding outcomes and our capacity to use talent and technology to propel business success. I have a strong interest in using cutting-edge technology and creative solutions to fulfill the constantly changing needs of businesses. In order to keep up with the latest developments, I am always looking for ways to improve my knowledge and abilities. Fast-paced work environments are my favorite because they allow me to use my drive and entrepreneurial spirit to produce amazing results. My outstanding leadership and communication abilities enable me to inspire and encourage my team and create a successful culture.